On April 12, 2018, two team members from Veliger, Biology major Eamon MacDonald and Writing, Rhetoric, and Technical Communications major Catie Willett, traveled alongside JMU Graduate Student Bailie Lavan and Industrial Design major Skylar Southard to Hudson, Florida to each test their separate oyster research projects on live oysters. The students were assisted by Dr. Josh Patterson of the University of Florida Forest Resources & Conservation department, who graciously provided the students access to reefs located in Hernando Beach.
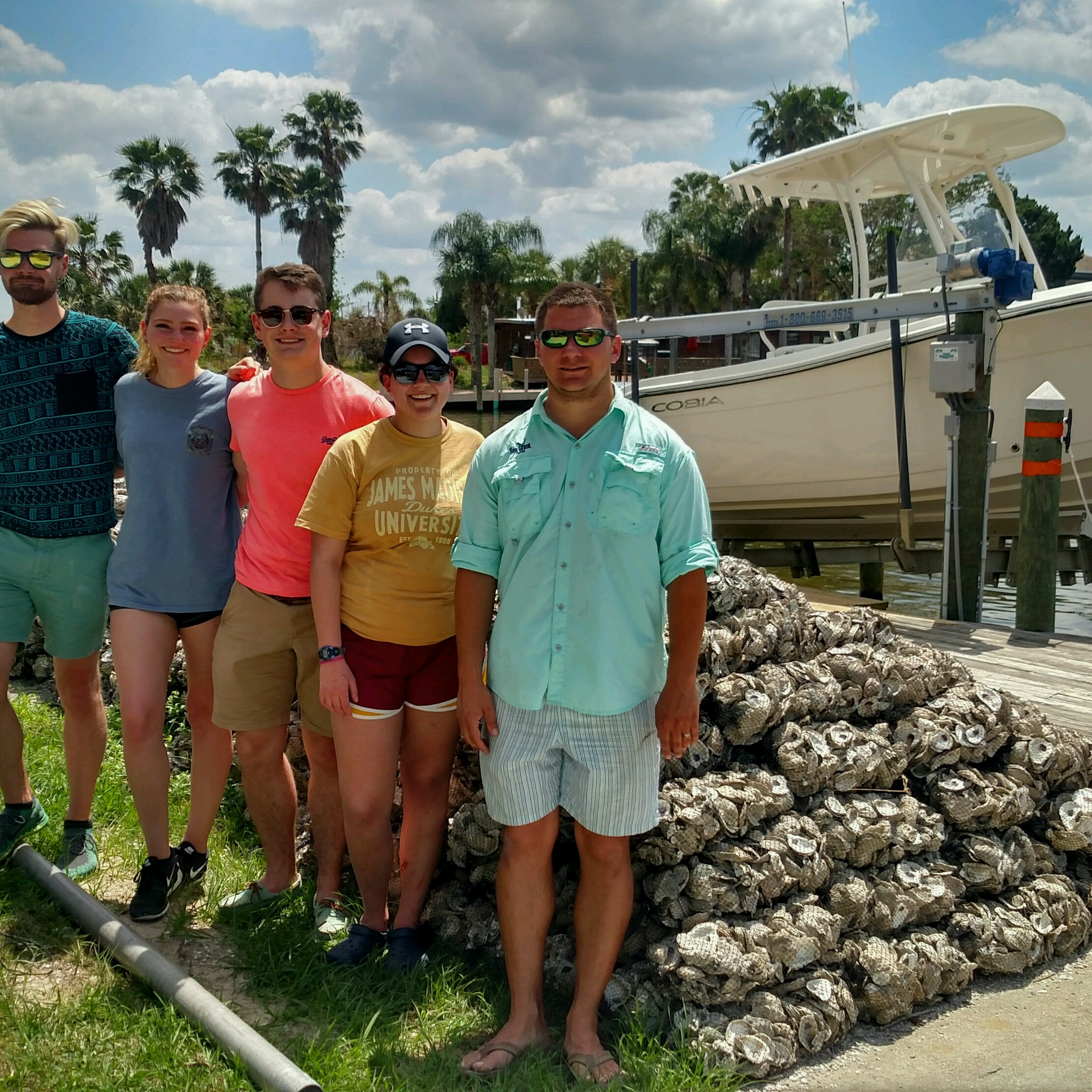
From left to right, Skyler Southard, Catie Willett, Eamon MacDonald, Bailie Laven, and Dr. Josh Patterson posing in front of 300 oyster bags.
For Veliger, the goal of the trip was to test the newly added front propeller on their underwater remote operated vehicle (ROV). The purpose of the additional propeller will be to remove excessive sediment found on existing oyster reefs in the Bay in an effort to reduce the number of oysters who suffocate from sediment coverage. After which, the students offered to assist in a community-wide oyster deployment in the Bay.
Day 1
April 13, 2018
The first day in Florida called for an early morning. The group arrived at Florida Sea Grant’s boat dock at 8 a.m. to meet with Dr. Patterson and explore Centipede Bay for a proper testing site. About 30 minutes out from the dock, the team found a large intertidal oyster reef, meaning the reefs were exposed upon low tide. Once the location was set, MacDonald and Willett began setting up the ROV.
The process of setting up the drone is a rather lengthy endeavor: first, the ROV needs to be attached to a large Alien Ware computer and manually connected without using WiFi, then the new propeller (which was being tested underwater for the first time) needed to be hooked up, code-tested, and sealed into a tupperware container sealed under the drone, and finally the GoPro Hero 4 needed to be hooked up to the drone and connected to a phone on the boat using a coaxial cable to obtain a live viewing of what the drone was seeing. This multi-step process has been practiced many times in the lab before, but this would be the first time setting up in the field.
Testing the ROV
The team began assembling the ROV by hooking it up to the Alien Ware computer; however, a major technical error occurred early on when the team could not get the drone to start. While the ROV is self-powered through six batteries, it requires connecting a small electrical board attached with an Ethernet and USB cable connected to a computer to power on the ROV. At first, when the drone did not turn on, the team assumed it was because the batteries were dead; however, after checking their battery life, they found the batteries to be fully charged.
The source of the technical error was actually from two very small wires. Again, the ROV requires connection to a computer via two cables, an Ethernet and USB cable. These two cables are connected to a small electrical board that functions like a translator, it communicates the connection between a computer and the ROV.
This information is delivered through the ROV tether comprised of two very thin, dainty wires. Unfortunately, these tiny wires consistently and easily disconnected from the small electric board. The wires are so delicate too that it is challenging to force them into place without damaging the wire. Thus, the ROV would not power on due to a communication error from the computer to the drone via the two tiny cables.
Additionally, the ROV is connected through an IP address (or its Internet address) via Google Chrome. Although the process of connecting the drone to Chrome does not require WiFi, there are still times when there isn’t a proper connection between the ROV and the computer. While on the boat, the team experienced both of these technical challenges, so they decided to manually direct the ROV underwater.
Testing the Propeller
After the drone was manually placed in the water, the team tried to use the attached propeller. Above water, the propeller worked well at a high speed, turning without a problem. However, when the propeller entered the water while turned on, it slowed significantly, still turning, but at a much lower speed. The team then tried to only turn on the propeller when the drone was fully submerged, however, the same effect happened where the propeller was slower than above water. After the propeller was used underwater, it would have a sputter start, even above water.
To see if the 3D printed propeller was the problem, the team tried two types of designs: first, a thick wheel-shaped propeller, then and thin wheel-shaped propeller. The thick propeller did prove to be too large for the motor itself, causing screws to come loose and the motor to slow. The thin propeller was then placed on and appeared to fit the motor better, allowing for full speed without any friction or problems from the surrounding area when above water.
However, when the small propeller was placed in the water, the motor slowed once again. The team speculates a few possible errors: either the connection between the Arduino and the motor became weak underwater, the water provided too much resistance on the motor, or a number of other reasons. The team plans to reassess this situation with JMU Physics professor Dr. Kevin Giovanetti upon their return to the X-Labs. After reviewing the propellers, the team next wanted to examine the GoPro images.
Testing the GoPro
GoPro results proved to be the most successful aspect of the test. Images were clear once the ROV was close to the reef and the live stream from the GoPro to a cell phone was successful using a coaxial cable. The team did find that since the GoPro was strapped to the top of the drone facing straight out, the ROV had to be tilted almost 90 degrees to successfully view the entire reef. Having the camera angled properly is an important facet, moving the camera to a lower spot on the ROV or tilting the camera 25 degrees could assist in easier image capturing.
Day 2
April 14, 2018
After testing on Day 1, the team returned to Centipede Bay the following day to assist in a community-wide oyster reef deployment. The event was hosted by University of Florida’s IFAS Nature Coast Biological Station at the Florida Sea Grant center where 50 volunteers from the community came to either donate their boats for transport of oyster shell or their time to assist in manually placing oyster bags in the Bay.
At the loading dock, there were 2,500 bags of oysters, each around 30 lbs, which is about four tons of oysters, each being loaded by 20 volunteers onto a number of pontoon boats and small fishing boats.
The bags of oysters were received by another group of volunteers positioned in the water of the Bay who were responsible for arranging the oyster bags by hand in a football-shaped pattern.
The event ran from 10 a.m. to 4 p.m. and by the end of the day, there were only 100 bags left on the dock and more than half of the oyster reef design was complete.
Veliger graciously thanks Dr. Patterson and Florida Sea Grant for hosting the team and allowing students to pursue their research through live field testing. The experience was groundbreaking for the team and provided significant insight into the project moving forward.